Special machine construction projects
Special machinery projects
Complexity and individual concepts combined
Special machinery projects are characterized by their complexity and individual design. Special machines offer specially developed solutions for specific customer tasks - often accompanied by the automation of parts or units.
Production of PVC window profiles
Hydraulic lightweight press
UD-Tape procedure
MACS - Autoclave
Production plant for the manufacture of
PVC window profiles
Project objective in detail
The main objective of the project is the construction and commissioning of a production plant for the manufacture of PVC window profiles by ERMAFA Sondermaschinen- und Anlagenbau GmbH. The aim is to produce up to 40,000 tons of window profiles per year.
Background and motivation
The client would like to use additional PVC production capacity to produce high-quality finished products such as window profiles in addition to the basic material. This offers the following advantages:
- Increasing added value: By converting raw PVC into finished window profiles.
- Market potential: Window profiles are in high demand, particularly in the construction and renovation sector.
- Diversification: Expansion of the product range and strengthening of the market position.
1. production efficiency:
- Ensuring continuous production in 4-shift operation (rolling week, 100% duty cycle).
- High system availability of 90-95 %.
- Minimization of maintenance times (5-10 % of the operating time).
- Maximization of production capacity to 40,000 tons of window profiles per year.
2. quality assurance:
- Production of high-quality window profiles that comply with standards (e.g. DIN EN 12608).
- Use of modern technology to ensure consistent product quality.
3. flexibility and expandability:
- The system is designed in such a way that it can be expanded with additional production lines if required.
- Use of modular systems to facilitate future adaptations.
4. safety and environmental standards:
- Implementation of high safety standards in accordance with occupational health and safety and fire protection regulations.
- Minimization of pollutant emissions and environmental pollution.
- Efficient use of resources (e.g. energy recovery through heat recirculation).
Technological implementation:
- Use of the latest extrusion and mixing technology.
- Central process control system for monitoring and controlling production.
- Automation of material supply and storage to reduce downtimes.
- Use of heat recovery systems to minimize energy losses.
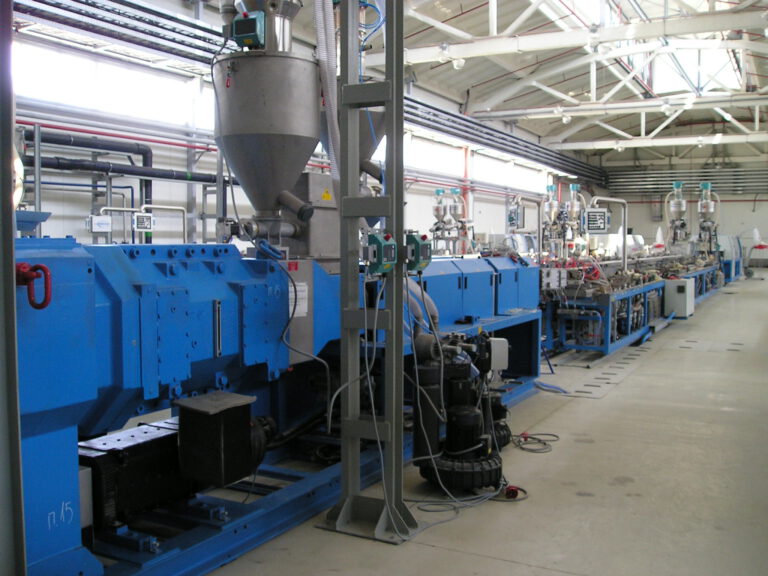
Expected benefits:
- Economic benefit
Higher profits through the marketing of finished window profiles. Cost savings through the use of existing PVC capacities.
- Technological lead
Use of state-of-the-art machines and control systems to increase efficiency and use energy-saving processes to conserve resources.
- Market opportunities
Supplying the booming DIY market with high-quality window profiles. Ability to react flexibly to customer requirements (e.g. special profile shapes).
The successful realization of the project offers a sustainable improvement in production efficiency and product quality and strengthens the client's market position by opening up new sales markets.
Production and operating data
- Duty cycle: 100 %
- Shift rhythm: 4-shift system (rolling week, no breaks)
- Availability: approx. 90-95 %
- Annual operating hours: 8,760 h (approx. 7,884-8,322 h effective)
Warehousing
- Storage area: approx. 450 m² with 316 pallets on three levels
- Raw materials:
- PVC-S, brand S, К 66-68: 81.23 %
- Filler (chalk, Omiacarb 95T): 8.12 %
- Colorant (titanium dioxide, Kronos 2220): 3,25 %
- Stabilizer (ІКА 7035C9G, Са-Zn): 3,09 %
- Modifier (Vinuran DS 2391, BASF): 4.31 %
Energy and water requirements
- Total energy requirement: 3,105 kW
- Cooling capacity: 625 kW/h, existing cooling capacity: 675 kW/h
- Compressed air requirement: 168 Ncbm/h (at 1 bar / 20°C / 0% humidity)
- Wastewater contamination: zinc 0.01 mg/l, cadmium 0.01 mg/l, lead 0.04 mg/l
Fire protection and occupational safety
- Fire protection measures: Fire alarm systems in accordance with DIN 14675, fire extinguishers in accordance with DIN EN 3
- Occupational health and safety: regular training and safety checks
- Hazardous substances: PVC as flame-retardant (DIN 4102), no high fire risk
Automation and control
- Central process control system for inventory control and warehouse management
- Automated ordering with minimum stock quantity
Personnel requirements
- Shift operation: Maximum 40 employees per shift
- Staff allocation: production and laboratory
Sustainability and energy saving
- Use of the energy generated during cold water treatment (300 kW) to heat the production hall
The plant for the production of PVC window profiles consists of the following machines and components:
1. component preparation
Component preparation includes the mixing and dosing of the raw materials required for the production of PVC window profiles. This includes
- Dosing systems: Precise dosing of raw materials such as PVC, fillers, stabilizers, modifiers and dyes.
- Dry mixer: Combines and homogenizes the components at room temperature.
- Heating mixer: Heats the mixture to improve homogeneity.
- Cooling mixer: lowers the temperature after mixing to prevent clumping.
2. heating/cooling mixer
This unit is a central component of PVC processing:
- Heating mixer:
- Operating temperature: approx. 120-140 °C.
- Output: approx. 200 kW/h.
- Task: Heating and plasticizing the PVC mixture.
- Cooling mixer:
- Power: approx. 30 kW/h.
- Task: Rapid cooling of the material after heating.
- Advantage: High homogeneity and consistency of the PVC mixture.
3. twin-screw extruder
The twin-screw extruder is the heart of the production line:
- Task: Melting and continuous discharge of the PVC material.
- Twin screw: Provides an even distribution of the material components.
- Temperature control: Keeps the melt at the optimum level (approx. 180-200 °C).
- Motor power: Depending on extruder size approx. 100-300 kW.
Equipment: Degassing unit for removing vapors.
4. profile tool
The profile tool shapes the melted PVC compound into window profiles:
- Material: High-quality steel for high precision and durability.
- Cooling channels: Prevent deformation during profile formation.
- Change options: Adaptable for different profile shapes.
5. calibration table
The calibration table ensures the dimensional stability of the extruded profile:
- Functions:
- Calibration: Ensures the exact geometry of the profiles.
- Cooling: Cools the profiles quickly to maintain a stable shape.
- Water cooling: With integrated circulation system (approx. 250 kW cooling capacity).
- Length: Depending on the profile size, usually approx. 6-12 meters.
6. caterpillar removal
The caterpillar haul-off pulls the profile continuously and evenly out of the extruder:
- Motor power: Typically approx. 5-10 kW.
- Speed control: Adapts to the extrusion rate.
- Drive: Belt drive with high grip to prevent slipping.
7. saw
The saw cuts the extruded window profiles to the desired length:
- Cutting length: Usually in the range of 3 to 6 meters.
- Saw type: Circular saws or band saws.
- Automation: Fully automatic adjustment to the profile speed.
8. storage table
The finished profiles are collected and stacked here:
- Conveyor belt: Automatic material flow from the fume cupboard to the storage area.
- Stacking: Optimized stacking technology to prevent damage.
Additional systems:
- Cooling water system: Closed circuit for heat reduction.
- Compressed air system: Supply of pneumatic controls and valves.
- Extraction systems: Dust and vapor extraction during the mixing and extrusion process.
- Process control system: Monitoring and control of the entire production line.
High performance even without a foundation
Hydraulic lightweight press
We were able to develop a special innovation in the field of forming together with IWC. The result was a hydraulic press that requires neither a foundation nor a basement.
This crucial aspect minimizes space requirements, improves the arrangement of machines and enables efficient workspace design. The quick installation without a foundation shortens the commissioning time and promotes a rapid start to production. The flexibility of location without a fixed foundation makes it easy to adapt the machine.
Unlike conventional hydraulic presses, we provide you with individual sizes designed for your specific applications. This minimizes the space required in the workshop and reduces both acquisition and running costs.
- Low maintenance and servicing costs, quick tool change
- Expansion of the market segment for formed parts through small batch sizes
- Low overall height, less space required
- Integration into assembly lines or other process chains possible
Potential

Load-bearing lightweight components using the UD tape process
UD tape system
UD tapes are continuous fiber-reinforced tapes with a thermoplastic matrix.
The product is thermoplastically moldable, lightweight and yet resilient.
The glass or carbon fibers of the UD tape are unidirectional and can be processed into multilayer components using pressing or thermal processes.
The tapes are manufactured using the patented direct impregnation process, which achieves a high degree of impregnation and a good bond between the fibers and the matrix material. The fiber content of the tapes can be flexibly adjusted for different areas of application.
In further process steps, the UD tape can be used to produce organic sheets and molded parts.
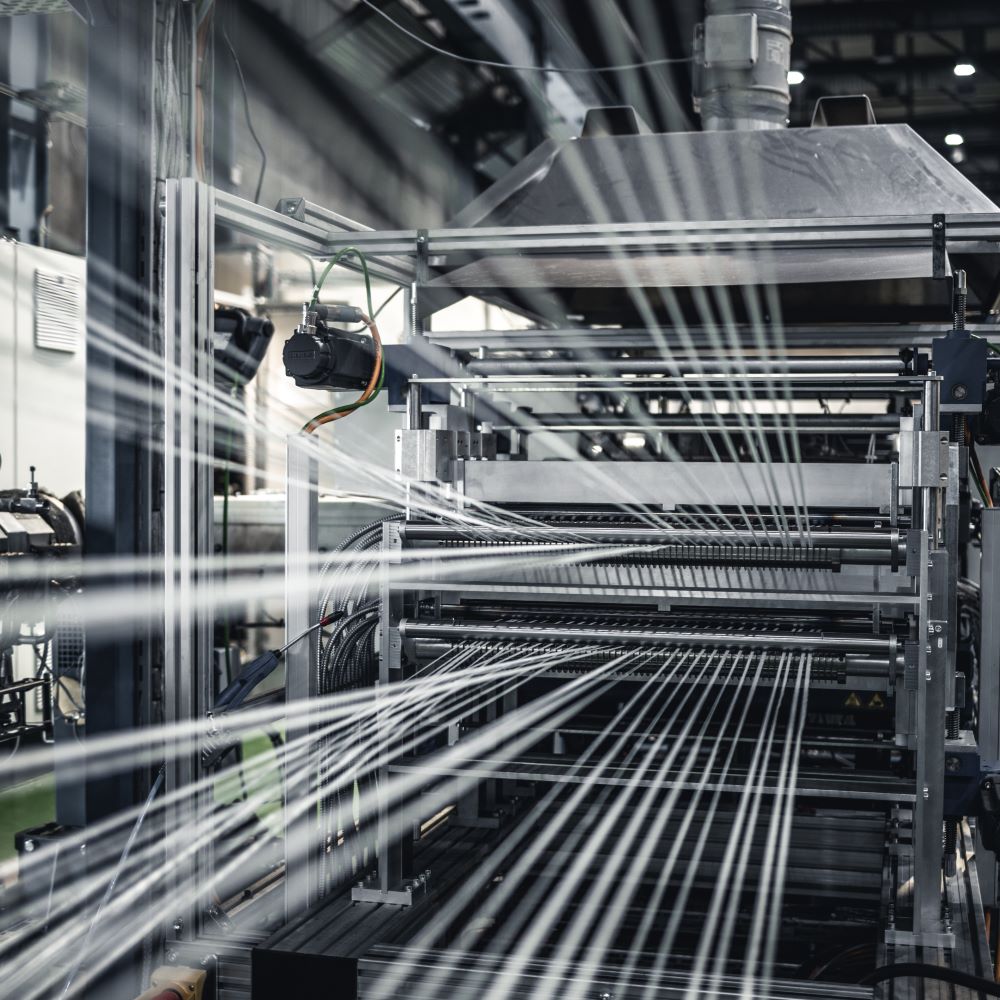
Potential
- High load-bearing capacity thanks to multiple layers
- Low component weight
- Suitability for thermoforming
- Higher recycling potential through thermoset solutions, for example
Mode of operation
The UD tape system produces a composite material from plastic melt and reinforcing fiber. The creel stores the reinforcing fiber, the fiber spreader forms a unidirectional fiber fabric. In parallel, a compounding line prepares the plastic melt in the extruder (ERMAFA twin-screw extruder). The melt pump transports the melt to the patented impregnation tool, where it is rolled into the fiber web. The components pass through a wide slot die to the 3-roll calenderwhich presses and smoothes them into a composite material. After cooling on the roller conveyor, the edge strips are trimmed and rolled up. The take-off device pulls the material off the calender and the rewinder rolls it up.
Safe treatment of infectious and hazardous waste
MACS - Machine Autoclave Cutting Sterilization
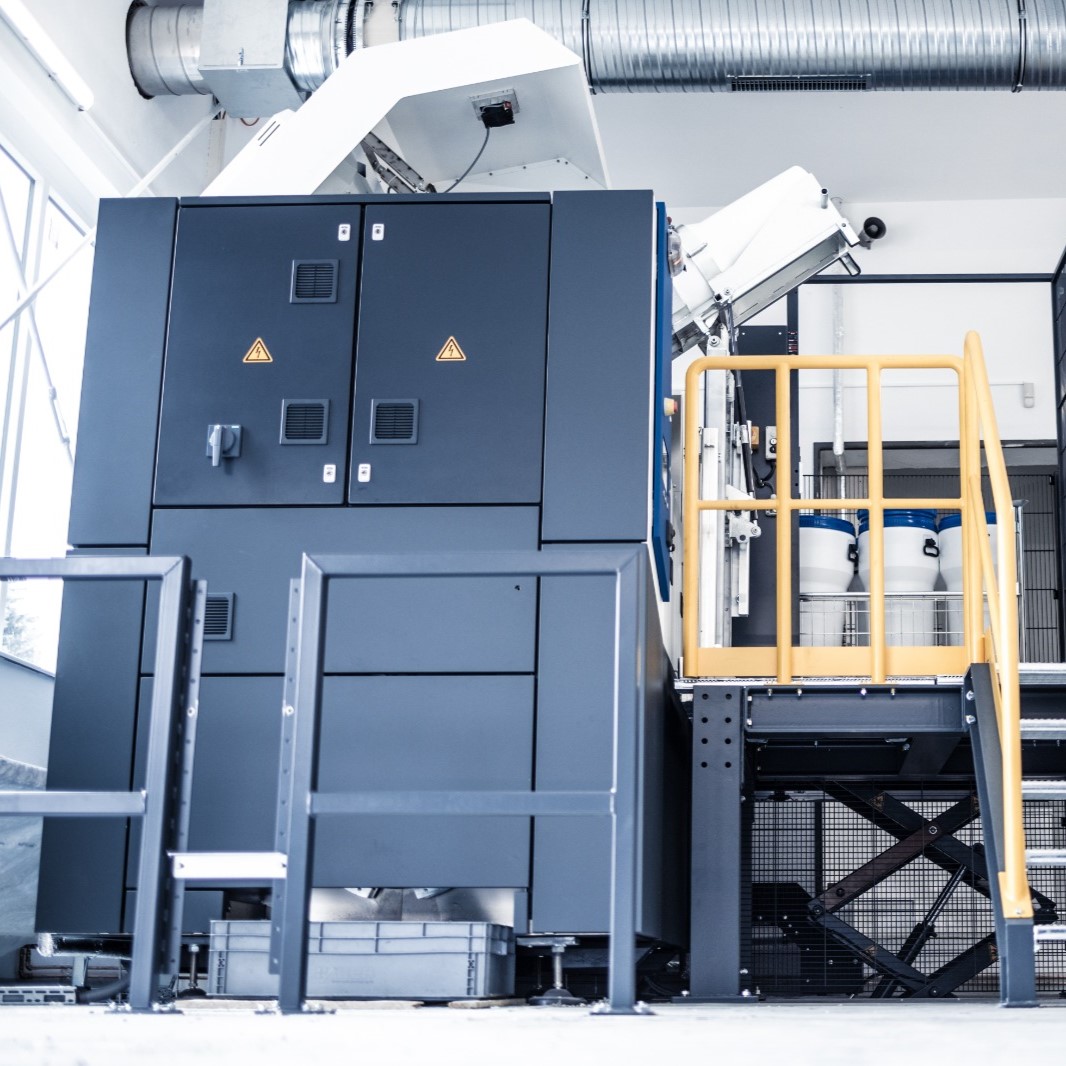
- On-site solution or industrial solution
- Customized design according to application
- Simple operating software
- Solids and liquid waste
Special features
These autoclaves for the treatment of contaminated waste provide enormous economic added value! Cross-contamination is eliminated through direct on-site treatment - which is safe for people and the environment.
In addition, cost-intensive transportation of hazardous goods is no longer necessary, which represents an enormous CO² saving potential.
Up to Safety Insurance Level SAL= 10high48 (WHO recommends 10-6)high10
Your contact person:
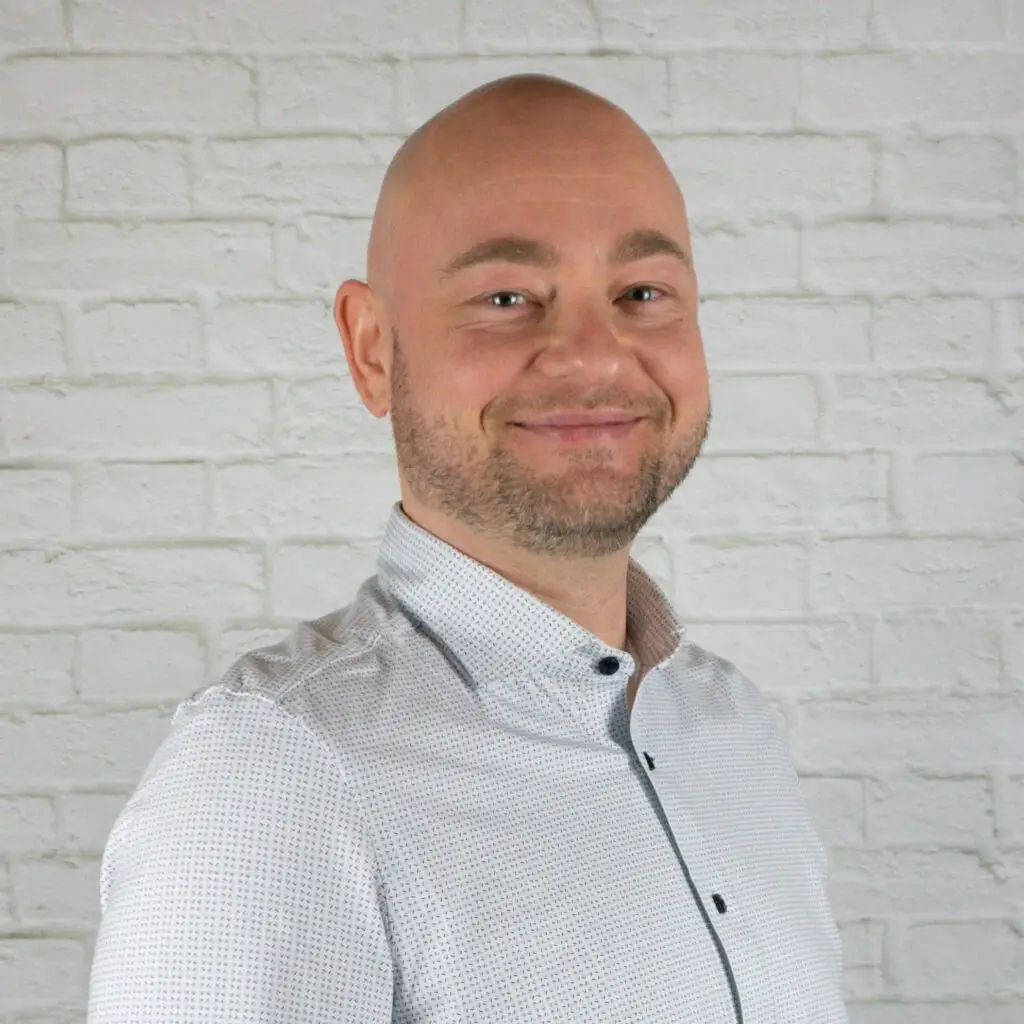